HC Plastics News:
We only need to add a very small amount of graphene to some plastics to significantly change the properties and properties of the plastic. In the promotion of the automotive industry, new technologies are always described as “revolutionaryâ€, but this is often a good wish, not everyone believes.
However, for an emerging material, this description is very objective as long as the word "may" is added before the "revolutionary". This is graphene, which is “probably†a “revolutionary†automotive technology.
Looking back, the graphene material was officially separated by researchers at the University of Manchester in the north of England in 2004. It is still only a new material that is only a "pregnancy", but has begun to steadily advance to mature mass production. In the next decade, graphene materials will likely bring significant changes to the design and manufacturing sectors, including the efficiency of electric vehicles and self-driving cars.
? ?
Versarien is an advanced materials engineering group led by Dr. Andrew Deakin as a Chief Technical Engineer. The company is dedicated to extending the application of graphene materials from theoretical research to actual production, allowing this emerging material to fully reduce weight, strengthen materials and optimize batteries. The role. “As long as it is used properly, I think graphene materials are expected to reduce the plastic part of the vehicle by 20%. This will be revolutionary. In addition, with excellent electrical conductivity, graphene materials are also expected to optimize battery performance, thus significantly extending the battery. Service life."
? ?
As an allotrope, graphene is a derivative of graphite (usually used in pencils and dry lubricants). At present, a large amount of research and development work is still required for the large-scale application of graphene materials to mass production of automobiles. Dr. Deakin has been working to promote the use of graphene in vehicle design and manufacturing, but at the same time frankly face the possible challenges: “The application of graphene in some scenarios may be realized in a few years, in other scenarios. Applications may take more than a decade, and the exact time is often difficult to judge, but I am confident in the potential of this material."
Forecasts show that by 2020, the global automotive industry may use up to 6 million tons of plastic per year , but the final amount may fluctuate: for example, if a stronger, lighter plastic is made by adding graphene and replaced For other materials with higher mass density, the final amount of plastic may increase.
Reinforced plastic
Dr. Deakin and his team are working to increase the strength of plastics by more than 30% to achieve the same amount of reduction but also achieve the same or higher strength. However, there are currently 13 types of plastics commonly used in vehicle manufacturing, and all types of plastics must undergo testing procedures.
Dr. Deakin said, “We have to determine how the graphene is added to the plastic, and the proportion of specific blends, such as 1% to 5%. Then we have to improve all the necessary processes and technologies; finally, we will optimize the comprehensive test, and then Promoting small-scale production to industrial scale.†Dr. Deakin has begun to use graphene materials to optimize the performance of tires, composite body panels, CFRP materials and batteries.
“In the initial stage, we have to find the most meaningful application scenarios, and because of this, we are looking for help from a large number of industry experts. For example, we can use graphene to extend tire life to the current level. 1.5 times, or even 2 times, and at the same time reducing the need for plastic particles in the manufacturing process, which is very meaningful for protecting the environment. A recent report pointed out that in the plastic waste that is less than 1mm in diameter and finally dumped into the ocean, there is More than 28% are from tires.†Graphene also helps to reduce the weight and size of the battery, which in turn can extend the range of electric vehicles and have the potential to increase the battery charging speed.
In addition, graphene can also improve the impact strength of plastic sheets or bumpers , and similar performance gains can be obtained when applied to vehicle chassis. Of course, in order to achieve the desired effect, it is also necessary to continuously optimize the mixing ratio of graphene. On the other hand, graphene is generally not used for the reinforcement of aluminum or steel, but "the direct use of graphene-reinforced plastics to replace these metals" is also an alternative idea.
Dr. Deakin explained: “If graphene-reinforced plastics are used, the torsional stiffness of the parts will remain the same, even increase, and the impact strength will increase. Therefore, it is expected that more and more scenes will begin to use quality in the future. Lighter plastic, CFPR and GRP materials."
Versarien acquired 2D Experts in 2014, when the latter produced only 1 gram of graphene per day. Today, with the introduction of new equipment, the company expects to increase its single-day graphene production to 1 kg later this year ( 2.2 lbs).
In this regard, Dr. Deakin said this is equivalent to a 1000-fold increase in production factors. In simple calculations, if the average daily production per machine can be increased to 10 kg (22 lbs), 100 units can increase the company's single-day production to 1 ton. Dr. Deakin added, “In addition, it is important to control the amount of graphene added to the plastic (possibly only 1% or less) when significantly optimizing the properties of the plastic.â€
Dr. Deakin's details on the graphene production equipment and how it works are just a few words, indicating that plastics manufacturers can easily install such equipment in existing production plants.
In Dr. Deakin's definition, "real" graphene contains only a single layer of single-layer carbon atoms. However, most of the scales of Versarien graphene materials are no more than 5 layers, 90% of the scales are no more than 10 layers, and the average lateral dimension is only 2 microns.
In addition, recyclability is an important issue that must be considered before any new material can be officially applied. Dr. Deakin believes that the advent of graphene will rejuvenate old plastics (for example, when plastics are degraded by ultraviolet radiation), that is, retain their original properties or properties and re-enter the supply chain.
However, we still have to face a long-standing problem: what is the cost-effectiveness of “reducing the plastic consumption of vehicles by adding graphene� Dr. Deakin said: "We expect that this graphene solution will be truly cost-effective in the next few years by using our technology, which takes about five years." Then, this layer of graphite with only one layer of atomic weight Can a olefin be a true "revolutionary" material? This will take time to verify.
Editor in charge: Honor
Poleline Construction Hardwares
Poleline construction hardware refers to the various components and equipment used in the construction and maintenance of power transmission and distribution lines. These hardware items are designed to support and secure the conductors, insulators, and other components of the poleline system. Some common examples of poleline construction hardware include:
Pole Line Fittings: These are various fittings and attachments that are used to connect conductors to the poles, insulators, and other components. Examples include pole brackets, crossarms, guy wire clamps, and pole bands.
Insulators: Insulators are used to support and isolate electric conductors from the pole or tower structure. They prevent the flow of electric current from the conductor to the ground. Insulators can be made of various materials such as glass, porcelain, or composite materials.
Anchoring and Guying Systems: These systems are used to provide stability and support to the poles or towers. They include guy wires, anchors, deadends, and turnbuckles.
Yokelink supply a full line of Poleline Hardware, we offer from the top of the pole to underground. Here are some of the pole line accessories that you are likely to use for your project
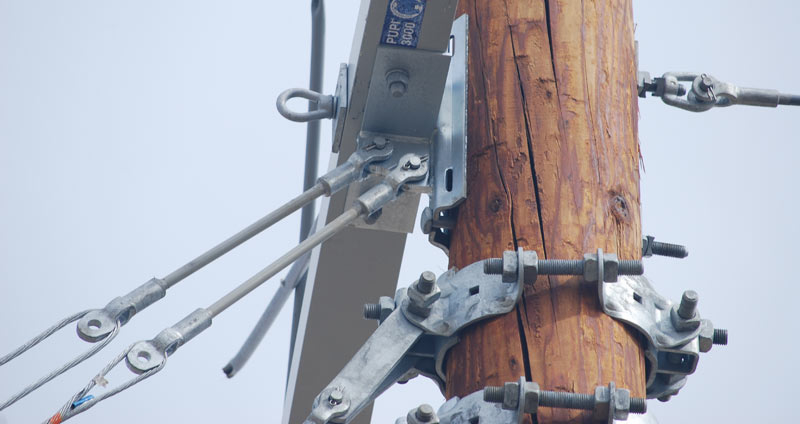
Yokelink Flat Crossarm Brace used to support wood cross arms carrying tangent loads. Round corners on the brace ends prevent damage and reduce the possibility of injury. Hot dip galvanized meet ASTM A153 specification.
Yokelink Alley Arm Brace used for side-arm construction, mounted to one side of the pole, mount at a 45 degree angle and come complete with solidly riveted lineman step. Hot dip galvanized meet ASTM A153 specification.
Yokelink Insulator Brackets are used to mount post type insulators from 15kv to 34.5kv on the side of the pole. Hot dip galvanized meet ASTM A153 specification.
Yokelink Cutout and Arrester Brackets are used for strength and mounting a variety of electrical equipment including arresters, cutouts, combination units and terminations. All components are Hot dip galvanized to meet ASTM A153 specification.
Clevis, Bracket,Transformer, Mounting, Brace, Crossarm, Cutout, Alley, Cross arm, Pole Band
Ningbo Yokelink Machinery Co.,Limited , https://www.yokelink.com