- Model NO.: HS-C3000 Pro
- Weight: 210g
- Installation Mode: Handheld
- Specification: CE, ISO9001; 2008
- Model No.: Hs-C3000 PRO
- Dimensions: 80 X 68X 31 Mm
- Certification: CE, FCC
- Origin: Shenzhen, China
C3000-Pro is the most advanced handheld digital frequency counter, which can measure the frequency of any digital , switches and analog signals, such as mobile phone, wireless remote control, car key, WIFI, radio, 1.2G/2.4G wireless camera , wireless microphone and so on. This machine has features like lightweight and easy operation.
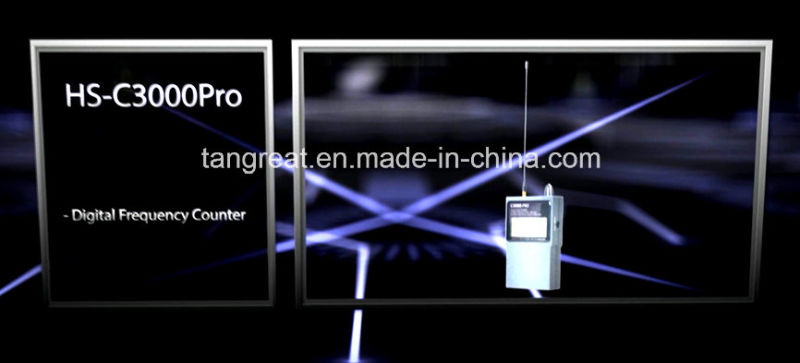
Product detailÂ
Features
1.8 LCD display
2 This machine can measure the frequency of any digital , switches and analog signals
3.16 extrasensory synchronous RF signal strength indicator (-35dBm to 0 dBm)
4 Temporary keys function , LCD display for easy reading
5. Test range keys function , LCD display
6 Squelch adjustment
7 Low-power 3 hours NiCd battery
8 High, medium and low battery LCD display
9 LED charge status indicator
10. Configured with full-band antenna and charging adapter
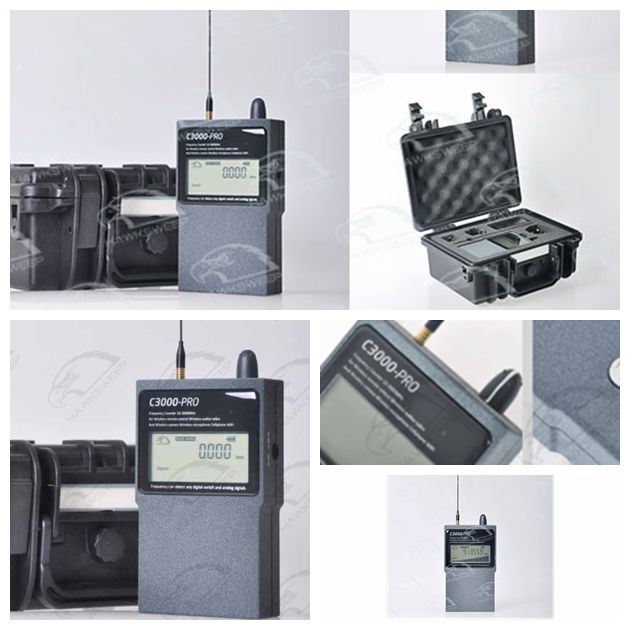
Technical Specification:
Resolution : 10 KHz ( digital or switch signal ) 1 KHz ( analog signal )
Time base :. <1 PPM typ room
Weight : 210 g
Dimensions : 80 mm (high) x 68 mm (width) x 31 mm (long)
Housing: gray aluminum housing
Battery : 7.4V2000 mAH Lithium polymer
Charger : 9 VDC, 1000 mA
Standard Configuration:
Device Host , battery, interchangeable plugs ( three ), charging adapter , a antenna .
Application
Â
Laboratory, communications engineering , electronic product testing
Serise Product :Â
WHAT IS SAND CASTING?
Sand casting is a versatile manufacturing process used to create metal parts by pouring molten metal into a sand mould.The process begins with the creation of a pattern, representing the final shape and dimensions of the part, which is then placed in a two-part sand mould. Once the mould is prepared, the pattern is removed, leaving behind a precise impression of the desired part. Molten metal is poured into the mould cavity, where it solidifies and takes on the shape of the part. After cooling, the sand mould is broken apart to reveal the metal casting inside.
At A & M Manufacturing Company Ltd. Our associated sand casting foundries are capable of producing a wide range of metal parts, from small components to large machinery parts, and can be used with both ferrous and non-ferrous metals. Examples of parts produced using this technique include engine blocks, cylinder heads, gears, pulleys, and ornamental metalwork.
SAND CASTING PROCESS
1. Pattern MakingThe first step is creating a pattern that represents the shape of the desired casting. Patterns are typically made from materials like wood, metal, or plastic and are designed to be slightly oversized to compensate for metal shrinkage during cooling. The pattern includes allowances for machining and draft, facilitating its removal from the mould.
2. Mould Making
The mould is made by packing special moulding sand around the pattern in a moulding box, known as a flask. The moulding sand is mixed with clay and water or other bonding agents to help it retain its shape. The process involves two halves of the mould: the cope (top half) and the drag (bottom half). The pattern is placed in the drag, and sand is packed around it. Then, the cope is placed on top, and sand is packed into it as well. Once the sand has been compacted, the pattern is carefully removed, leaving a cavity that mirrors the shape of the pattern.
3. Core Making
If the casting requires internal cavities or undercuts, cores made of sand are used. These cores are formed in separate core boxes and are positioned in the mould cavity before the molten metal is poured. They remain in place during casting to form the internal features of the part.
4. Melting and Pouring
The metal, which can vary from iron, steel, aluminium, bronze, and more, is melted in a furnace to a specific temperature. Once the metal reaches the desired temperature and is thoroughly molten, it`s carefully poured into the mould cavity. Pouring must be done at a controlled rate to avoid turbulence and splashing, which can create defects in the casting.
5. Cooling
After the molten metal has been poured, it begins to cool and solidify within the mould. The cooling time can vary based on the metal used and the size of the casting. It`s crucial to allow the metal to cool completely to ensure the integrity and strength of the casting.
6. Mould Breakaway
Once the metal has solidified, the sand mould is broken apart to release the casting. This step is irreversible; moulds made from sand are destroyed during the casting removal, meaning a new mould is needed for each casting.
7. Cleaning and Finishing
The casting is then cleaned of any sand, scale, and excess metal from the gates, runners, and risers used to channel the molten metal into the mould. Cleaning can involve processes like shot blasting, grinding, and cutting. Further finishing processes, such as machining, painting, or coating, may be applied to achieve the desired surface finish and dimensional accuracy.
8. Inspection
Finally, the casting undergoes various inspections for quality assurance, including dimensional accuracy, surface finish, and structural integrity. Non-destructive testing methods such as X-ray, ultrasonic, or magnetic particle inspection may be used to detect internal defects.
Sand Casting Aluminum,Green Sand Casting,Sand Casting,Sand Casting Stainless Steel
A & M Manufacturing Company Ltd , https://www.am-manufacturing.com