Another common way to increase the feed is to increase the feed rate by using a tool with more teeth. The feed rate of the insert is often limited to a certain range due to the influence of the thickness of the insert or the surface quality. The method of using a fine-tooth cutter or other more teeth can improve the cutting speed and feed rate without changing the cutting speed and feed rate. Give speed. Taking two multi-tooth reaming tools as an example, Sandvik Coromant's three-tooth reaming tool can increase the feed rate by 50% compared to the common two-tooth reaming tool; Kennametal is used for The number of teeth of an unadjustable reaming tool processed by an automobile cylinder is up to seven, and the machining efficiency is 350% of the common two-tooth reaming tool.
3. Large depth cutting
Large depth cutting is also very effective for improving machining efficiency. In the case of large machining allowance, the use of large depth of cut processing can effectively reduce the number of passes, thereby increasing the metal removal rate.
For large depths of cut, the stress conditions of the tool will deteriorate. A large amount of load is concentrated on the cutting edge, which puts higher demands on the toughness of the tool. Therefore, the tool material at this time should have higher toughness, the chamfering and rounding of the cutting edge, the support of the blade to the blade, and the support of the clamping system to the shank must be strengthened. At the same time, the selection of reasonable tool geometry parameters, such as reducing the lead angle to avoid excessive concentration of cutting loads, must always be considered.
Large depths of cut often result in large cutting power requirements, and application should pay attention to whether the machine and other parts of the process system can meet their power requirements. At the same time, the large cutting depth processing also has certain requirements on the tool structure. For example, the single-sided negative-type insert is superior to the double-sided negative-type insert, the vertical-mounted insert is superior to the horizontal-mounted insert, etc., and the professional cutter technician can be consulted.
4. Interaction
The following example achieves a competitive advantage by simultaneously increasing cutting speed and feed rate. The tool used by the tool user was a 12-tooth milling cutter with a cutting speed of 257 m/min, a feed of 0.13 mm per tooth (1.56 mm per revolution) and a blade life of 60 pieces. The new milling cutters for this user are 8-tooth milling cutters, each of which costs 26% more than the original. There is no competitive advantage. However, the new milling cutter can increase the cutting speed to 337m/min and the feed rate to 0.22mm (1.76mm per revolution). The interaction between the two increases the actual machining efficiency by 50%. At the same time, the new milling cutter has a 50% longer life than the original tool. The result of the improvement is that the user can save about $62,000 a year.
Second, reduce non-processing time
In the manufacturing process, the proportion of time spent on machining is often very limited. According to the information of the China Knife Association, even if some production tasks are very full, the production equipment is highly CNC-controlled, and the management is relatively advanced, the actual machining time of CNC machine tools does not exceed 30%. Therefore, how to reduce non-processing time is also an important aspect to improve processing efficiency. Here is a brief description:
1. Reduce processing steps
Sometimes the processing can be reduced by using reasonable techniques. For SE nails of Kennametal, the cylindricity of drilling is much higher than that of ordinary drills. In some cases, the reaming process can be eliminated. For example, direct milling of hard molds can greatly reduce the number of processing steps and shorten the mold manufacturing cycle. An example is the machining of a hole in a nickel-based alloy. The original machining was performed in three steps using a centering drill, a high-speed steel drill and a reamer. The SE drill bit made of K715 carbide is now used. High strength and anti-adhesive wear resistance, cobalt content up to 9.5%, uncoated), no need for center drill and reamer, no need to retract the tool when drilling, the production is very stable, the positioning of the hole is very it is good. More importantly, the cutting speed was increased from the original 8.54m/min to 22.88m/min, the tool life was increased from 18 holes to 150 holes, and the machining time was reduced from the original 54 seconds to 5.1 seconds, which was reduced by more than 90. At % time, the processing efficiency is significantly improved.
Previous Next
Fiberglass Backing Pad is mainly used for making flap discs, Clean And Strip Disc, wool felt disc, non woven flap discs, diamond Flap Disc and other abrasive discs
Flap disc backing pad Type: T-27 – Flat shape, T-29 – Conical or Tapered shape
Flap disc backing plate Material: Best quality fiberglass farbic, Excellent phenolic resin, Galvanized metal rings, Backing Flap disc nylon pad surface: Black paper or non-woven cloth
Advantanges:
1. All raw material are adopted with good quality, best quality fiberglass fabric, phenolic resin.
2. From 75~220mm various sepcification of fiberglass backing plate products are available here.
3. For your different requirement, we have diferent layer, shape products for your requirement.
4. Suitable for flap disc, flet disc, clean & strip disc, non-woven flap disc and so on.
Features:
1. High Quality Fiberglass Cloth with Phenolic Resin
2. High-strength fiberglass cloth with good flexibility, light-weight
3. Excellent bonding property and heat resistance
4. Strict detection, full inspection and random testing before shipping
Packing :
For regular order, we packed 100pcs/shrink and 1000pcs/carton, 30cartons on a pallet with plastic fully shrinked outside to avoid moisture.
But we can offer special packing as per customer's needs.
For fiberglass backing pad, the related products we supply is Abrasive Flap Disc , Flap Disc Adhesive , clean and strip disc, nylon fllap wheels, Bonded Abrasives , and Surface Conditioning Product, this is also our main best selling goods all over the world.
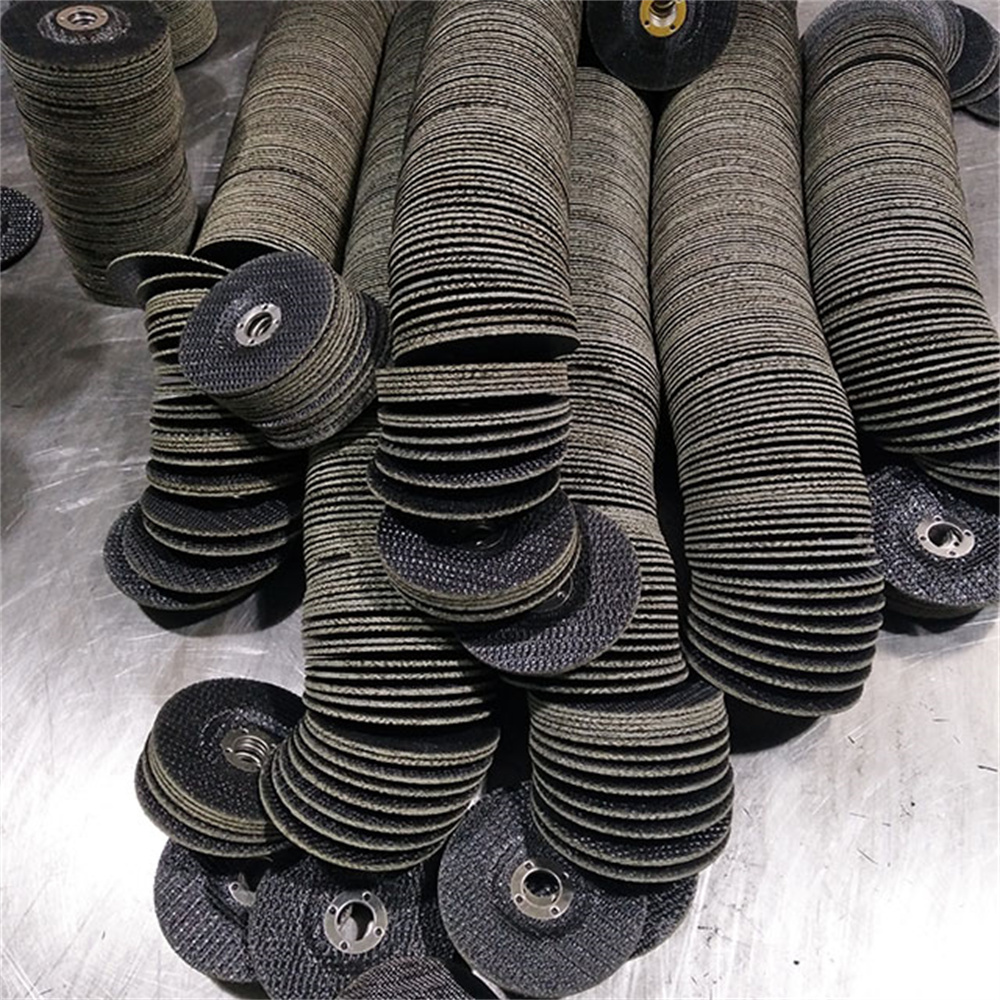
Flap Disc Backing Pad,Flap Disc Backing,Flap Disc Nylon Pad,Nylon Fiber Backing Pad,Plastic backing plate for flap disc
Zhengzhou Jiading Abrasive Manufacturing Co.,Ltd , https://www.jiadingabrasive.com