First, to improve the structure of the kiln is the basis for energy saving. The structure of the kiln is reasonable or not. It involves not only the consumption of fuel, but also has a direct relationship with the quality of the product. With a well-structured furnace, the smooth circulation of air and proper pressure in the kiln will greatly extend the life of the furnace. The structure of the kiln has been improved through continuous improvement. A new type of oil-fired (0# light diesel) shuttle kiln has four or six pieces (number depending on the size of the kiln) jet high-speed water passage in the same horizontal plane in the kiln. The combustion chamber of the gas-fired (liquefied petroleum gas) shuttle kiln has moved from the wall of the kiln to the wall products, changing the structure of the combustion kiln, and facilitating the direct injection of flame into the kiln under high-velocity injection, breaking the traditional ceramic kiln In a working state dominated by natural flow, pressure is used to induce high-velocity air jets to recirculate the air flow to form turbulent flow, strengthen the convective heat transfer process of the flue gas, increase the temperature in the kiln, and make the products appear fast and even. Heating saves fuel consumption.
The kiln should have a reasonable size. The size of the kiln is large, the heat dissipation area per unit product is small, and the heat consumption is small; the size of the kiln is too large, the temperature in the kiln is not easily uniform, the firing time is long, and the heat consumption is increased. If the product structure and loading method are not changed, the same volume furnaces with different lengths, widths and heights of the kiln have different firing times and fuel consumption. According to actual calculations, if the height of the shuttle kiln is increased by 50mm, the temperature difference between the upper and lower sides is increased by 30°C, the firing time is increased by half an hour, and the fuel consumption is increased by 5-8% per kilogram. On the contrary, if the length and width of the kiln increase and the height decreases, the same volume will not occur in the firing effect. Therefore, when the furnace is designed, the length and width of the kiln can be appropriately increased without affecting the product variety and production scale, and the height should be lower. In this way, the temperature difference between the upper and lower parts of the kiln can be reduced, and the firing time can be shortened to save fuel.
Second, to strengthen the seal of the kiln is to ensure energy-saving kiln sealing performance is good or bad, a direct impact on the size of fuel consumption. The heat storage capacity of lightweight foam insulation bricks and aluminosilicate fireproof fiber blankets used in the construction of kilns is only about 10% of that of refractory bricks. The above kiln wall and kiln roof are constructed with the above heat insulation material, the heat insulation performance of the kiln is good, and the outer iron combustion chamber is exposed at the high temperature stage. After being measured by a surface thermometer of WREA-890M, the temperature is only 50-80°C, which can reduce the fuel consumption by 10 -15%. However, the use of lightweight foam insulation bricks and shuttle kiln furnaces made of aluminosilicate fireproof fiber felt, although the one-off construction cost is high, due to significant energy-saving effect, within a few months after production, The cost of construction can be recovered.
The kiln car and kiln body of the ceramic shuttle kiln are enclosed in a zigzag and sand seal structure. The joints of the kiln car, the periphery, the periphery of the kiln and the contact of the kiln body are bonded together with a 30mm thick aluminosilicate refractory fiber felt, effectively preventing the Kiln flue gas temperature and cold air infiltration, increase the sealing performance of the kiln, reduce the temperature difference between the upper and lower furnace, reduce heat loss, shorten the high heat holding time, and promote the reduction of fuel consumption.
Third, adding heat exchangers to enhance waste heat recovery Shuttle kiln flue gas up to 1200 degrees is very worthwhile use. However, the traditional metal heat exchanger is unable to operate normally for a long time in a flue with a high temperature due to the limitation of its own material; in addition, a large amount of acidic substances in the exhaust gas also erode the heat exchanger from time to time. In this way, the metal heat exchanger is scrapped after being used once, and the company is wasting some of the open money. Does this mean that the heat exchanger is useless in the shuttle kiln? Is it possible to lose a large amount of energy that can be used blindly? the answer is negative.
Ceramic heat exchangers can solve these problems and make waste heat use reasonable. The use of ceramic heat exchangers is direct, simple, fast, efficient, environmentally friendly and energy-efficient. The ceramic heat exchanger is placed close to the exit of the flue and the temperature is higher. No need for cold wind and high temperature protection. When the furnace temperature is 1250°C-1650°C, the flue outlet temperature is about 1000°C-1350°C. Left and right, can preheat the air to 300 °C -750 °C, or higher temperature, using 300 °C -750 °C hot air and gas to form a mixture to burn, can save 25% -45%, or even more energy . It not only improves the work efficiency of the company, but also reduces the production cost.
Fourth, develop a reasonable operation program Take building sanitary ceramics as an example:
The firing of building sanitary ceramic products should be based on the characteristics of the billet, glaze, furnace structure, fuel types, etc. to develop a reasonable firing system and operation program. When firing, attention should be paid to mastering the three firing stages of oxidation flame, reducing flame, and neutral flame. Due to different flame requirements, the temperature and atmosphere are different, and the amount of fuel is different. If the reburning flame is burned too early or the amount of fuel is too large, it will not only cause defects such as smoking, but also cause unnecessary waste of fuel. Therefore, in the operation of product firing, the fuel consumption of each stage should be determined according to factors such as the structure of the furnace, the temperature difference in the kiln, and the size, thickness, dryness and humidity of the product, the requirements of the sintering temperature range, and the high heat holding time. Specific operations should pay attention to the following points.
(1) In the stage of ignition at 1050°C, it should be an oxidation stage, and the temperature increase rate should be 210°C/hour. At this stage, the amount of fuel is small to large, and the total oxidation is controlled. No carbon monoxide should be observed from the observation hole, and the flame in the kiln should be completely clear. The heating time is 4.5-5 hours.
(2) At the stage of 1050°C to 1360°C, it should be a reductive flame stage. At this time, the amount of fuel used to control the existing fire hole observed 250 ~ 300mm long flame (liquor liquefied petroleum gas kiln flame slightly shorter), indicating that the kiln reducing atmosphere is sufficient. When the temperature of the kiln top reaches above 1250°C, it can be turned into a high-temperature fire. When the high-temperature insulation is used, the fuel can be saved by firing at a relatively high temperature (ie, the upper limit of the sintering range) for a short period of time. General reduction time 2-2.5 hours, high fire holding time of half an hour, you can reach the requirements of the fired product
Pingxiang Tianma Industrial Ceramics Co., Ltd. of Jiangxi Province adopted this kind of advanced shuttle kiln for production. The shuttle kiln opened two doors front and rear, equipped with two kiln cars, one was sintered in the kiln, and the other was a loading and unloading truck. . Before the kiln is not cooled down, the kiln car will be loaded and heated in the kiln.
The kiln car runs steadily (it does not require trolley transfer), and the two kiln cars run alternately quickly, shortening the sintering cycle of the kiln and saving fuel in the kiln.
This type of gas drawer kiln is mainly used in ceramics, refractory materials, grinding wheels, zirconium-containing nozzles, industrial ceramics and other firing processing.
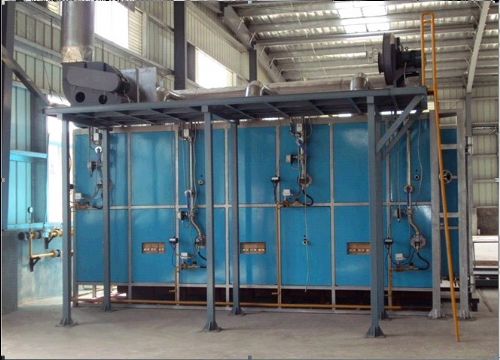
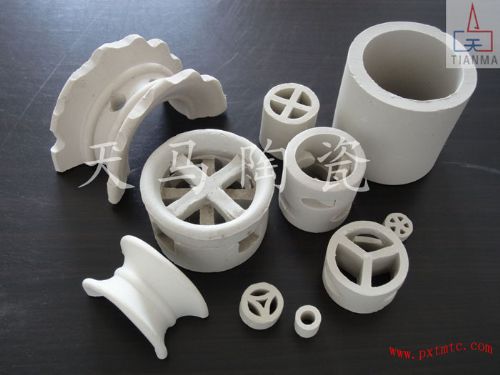
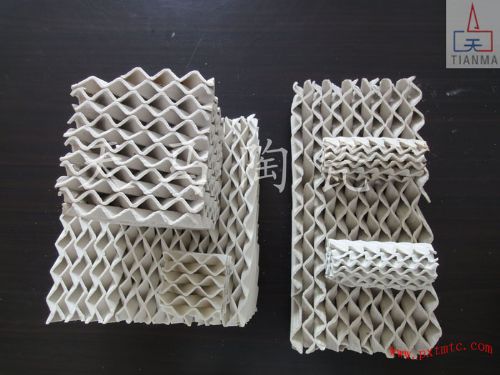
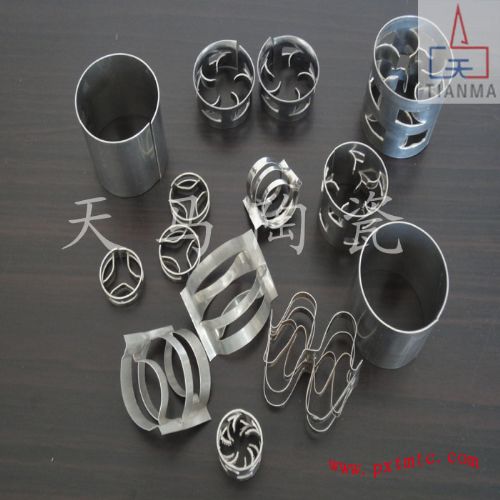
The kiln should have a reasonable size. The size of the kiln is large, the heat dissipation area per unit product is small, and the heat consumption is small; the size of the kiln is too large, the temperature in the kiln is not easily uniform, the firing time is long, and the heat consumption is increased. If the product structure and loading method are not changed, the same volume furnaces with different lengths, widths and heights of the kiln have different firing times and fuel consumption. According to actual calculations, if the height of the shuttle kiln is increased by 50mm, the temperature difference between the upper and lower sides is increased by 30°C, the firing time is increased by half an hour, and the fuel consumption is increased by 5-8% per kilogram. On the contrary, if the length and width of the kiln increase and the height decreases, the same volume will not occur in the firing effect. Therefore, when the furnace is designed, the length and width of the kiln can be appropriately increased without affecting the product variety and production scale, and the height should be lower. In this way, the temperature difference between the upper and lower parts of the kiln can be reduced, and the firing time can be shortened to save fuel.
Second, to strengthen the seal of the kiln is to ensure energy-saving kiln sealing performance is good or bad, a direct impact on the size of fuel consumption. The heat storage capacity of lightweight foam insulation bricks and aluminosilicate fireproof fiber blankets used in the construction of kilns is only about 10% of that of refractory bricks. The above kiln wall and kiln roof are constructed with the above heat insulation material, the heat insulation performance of the kiln is good, and the outer iron combustion chamber is exposed at the high temperature stage. After being measured by a surface thermometer of WREA-890M, the temperature is only 50-80°C, which can reduce the fuel consumption by 10 -15%. However, the use of lightweight foam insulation bricks and shuttle kiln furnaces made of aluminosilicate fireproof fiber felt, although the one-off construction cost is high, due to significant energy-saving effect, within a few months after production, The cost of construction can be recovered.
The kiln car and kiln body of the ceramic shuttle kiln are enclosed in a zigzag and sand seal structure. The joints of the kiln car, the periphery, the periphery of the kiln and the contact of the kiln body are bonded together with a 30mm thick aluminosilicate refractory fiber felt, effectively preventing the Kiln flue gas temperature and cold air infiltration, increase the sealing performance of the kiln, reduce the temperature difference between the upper and lower furnace, reduce heat loss, shorten the high heat holding time, and promote the reduction of fuel consumption.
Third, adding heat exchangers to enhance waste heat recovery Shuttle kiln flue gas up to 1200 degrees is very worthwhile use. However, the traditional metal heat exchanger is unable to operate normally for a long time in a flue with a high temperature due to the limitation of its own material; in addition, a large amount of acidic substances in the exhaust gas also erode the heat exchanger from time to time. In this way, the metal heat exchanger is scrapped after being used once, and the company is wasting some of the open money. Does this mean that the heat exchanger is useless in the shuttle kiln? Is it possible to lose a large amount of energy that can be used blindly? the answer is negative.
Ceramic heat exchangers can solve these problems and make waste heat use reasonable. The use of ceramic heat exchangers is direct, simple, fast, efficient, environmentally friendly and energy-efficient. The ceramic heat exchanger is placed close to the exit of the flue and the temperature is higher. No need for cold wind and high temperature protection. When the furnace temperature is 1250°C-1650°C, the flue outlet temperature is about 1000°C-1350°C. Left and right, can preheat the air to 300 °C -750 °C, or higher temperature, using 300 °C -750 °C hot air and gas to form a mixture to burn, can save 25% -45%, or even more energy . It not only improves the work efficiency of the company, but also reduces the production cost.
Fourth, develop a reasonable operation program Take building sanitary ceramics as an example:
The firing of building sanitary ceramic products should be based on the characteristics of the billet, glaze, furnace structure, fuel types, etc. to develop a reasonable firing system and operation program. When firing, attention should be paid to mastering the three firing stages of oxidation flame, reducing flame, and neutral flame. Due to different flame requirements, the temperature and atmosphere are different, and the amount of fuel is different. If the reburning flame is burned too early or the amount of fuel is too large, it will not only cause defects such as smoking, but also cause unnecessary waste of fuel. Therefore, in the operation of product firing, the fuel consumption of each stage should be determined according to factors such as the structure of the furnace, the temperature difference in the kiln, and the size, thickness, dryness and humidity of the product, the requirements of the sintering temperature range, and the high heat holding time. Specific operations should pay attention to the following points.
(1) In the stage of ignition at 1050°C, it should be an oxidation stage, and the temperature increase rate should be 210°C/hour. At this stage, the amount of fuel is small to large, and the total oxidation is controlled. No carbon monoxide should be observed from the observation hole, and the flame in the kiln should be completely clear. The heating time is 4.5-5 hours.
(2) At the stage of 1050°C to 1360°C, it should be a reductive flame stage. At this time, the amount of fuel used to control the existing fire hole observed 250 ~ 300mm long flame (liquor liquefied petroleum gas kiln flame slightly shorter), indicating that the kiln reducing atmosphere is sufficient. When the temperature of the kiln top reaches above 1250°C, it can be turned into a high-temperature fire. When the high-temperature insulation is used, the fuel can be saved by firing at a relatively high temperature (ie, the upper limit of the sintering range) for a short period of time. General reduction time 2-2.5 hours, high fire holding time of half an hour, you can reach the requirements of the fired product
Pingxiang Tianma Industrial Ceramics Co., Ltd. of Jiangxi Province adopted this kind of advanced shuttle kiln for production. The shuttle kiln opened two doors front and rear, equipped with two kiln cars, one was sintered in the kiln, and the other was a loading and unloading truck. . Before the kiln is not cooled down, the kiln car will be loaded and heated in the kiln.
The kiln car runs steadily (it does not require trolley transfer), and the two kiln cars run alternately quickly, shortening the sintering cycle of the kiln and saving fuel in the kiln.
This type of gas drawer kiln is mainly used in ceramics, refractory materials, grinding wheels, zirconium-containing nozzles, industrial ceramics and other firing processing.
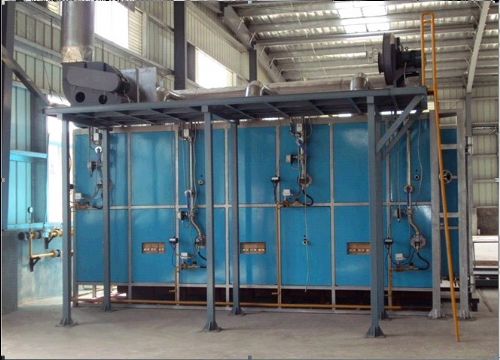
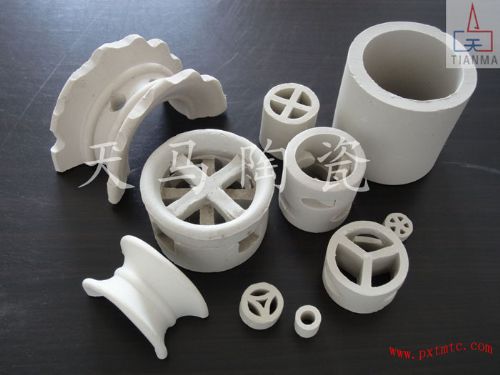
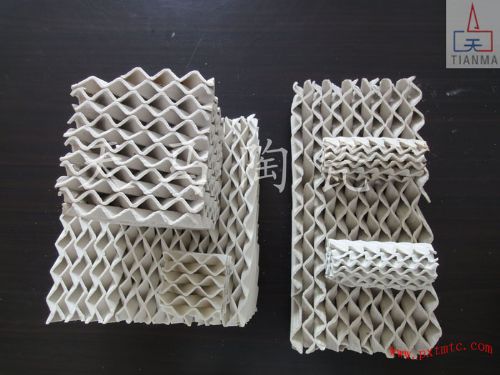
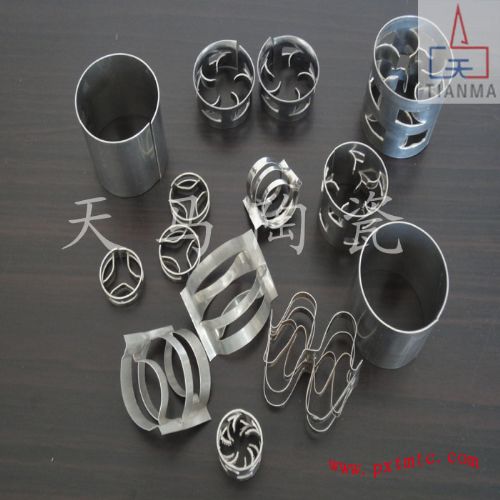
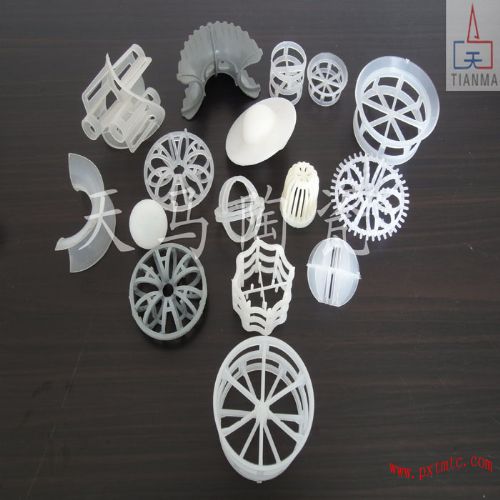
Cutting board
A cutting board is a must-have item in the kitchen. Cutting vegetables, cutting fruits, etc. are all inseparable from a useful cutting board. Our cutting board is made of selected natural wood, moderately soft and hard, tough and thick; not easy to hurt the knife, not easy to deform, not easy to burst, easy to clean; simple in shape, beautiful and durable, it is a rare kitchen helper.
Cut Board,Large Cutting Board,Vegetable Cutting Board,Teak Cutting Board
Jiangmen MEIAO Kitchen And Bathroom Co., Ltd. , https://www.meiaosink.com