During the heat treatment of large forgings, the temperature field and the distribution of the microstructure and its variation are extremely uneven, so that large transient stresses and residual stresses are generated, which in turn causes large deformation or even cracking of the workpiece. Computer numerical simulation technology can reveal the transient temperature field, tissue change, internal stress or deep concentration change inside the part during heat treatment, which gradually shows the guiding value in industrial production. The change of the internal temperature of the part during the heat treatment causes the phase change, and the latent heat of the phase change affects the temperature field of the part. At the same time, the temperature change and the phase change also cause the stress field inside the part. Therefore, the temperature-phase change-stress must be used in the simulation of the heat treatment process. / Strain three-coupled algorithm. The computer simulation technology of heat treatment process has been rapidly developed at home and abroad in recent years. The software used in the simulation includes general finite element software such as ABAQUS, ANSYS, MARC, as well as Japan's HEARTS, US DERFORM-HT, Sweden's TRAST, and China's Tsinghua University. NSHT, Shanghai Jiaotong University's SJTU-CARBCAD and other professional software.
Quenching heating temperature and holding time are important factors affecting the mechanical properties after heat treatment. Excessive heat treatment for quenching will cause coarse grains of austenite or cause overheating. The coarse grain of austenite during overheating not only reduces the mechanical properties, but also causes deformation and cracking. However, the holding time is insufficient, the carbide is not dissolved sufficiently, and the concentration of carbon and alloying elements in the austenite is low, which also causes the mechanical properties to decrease after heat treatment. In this paper, DERFORM-HT software is used to simulate the change of temperature field, microstructure field and stress field of large forgings of low carbon alloy steel during quenching heating process. According to the simulation results, the law of quenching heating process of forgings is predicted and revealed, so as to heat the holding time. The selection provides a basis for optimizing the process, shortening the production cycle and reducing production costs.
Simulation process
(1) Modeling The three-dimensional model of the rotary body was established using Pro-E software. The outer diameter of the rotary body was 620 mm and the axial length was 850 mm. The slewing body is axisymmetric. To simplify the calculation time, the 1/18 model is selected and imported into DERFORM-HT, and 20,000 cells are divided (see Figure 1) for numerical simulation analysis.
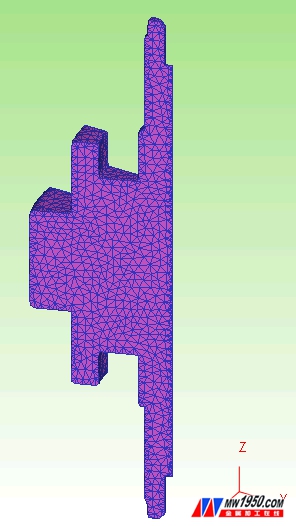
Figure 1 3D model of the body of revolution
(2) Material selection The material of the rotary body is alloy steel 20Cr2Ni4, BS-655M13 steel in DERFORM-HT numerical analysis selection software database, its alloy composition is close, C and Cr content are slightly different, see Table 1.

(3) Heat treatment process The process parameters of the quenching treatment of the rotating body are as follows: heating in the air resistance furnace, quenching temperature 850 °C, temperature setting stage at 450 ° C, 650 ° C respectively set insulation step 2h, 650 ° C temperature rise rate 50 ° C / h, 650 The temperature rise rate above °C is 100 °C / h. Taking 850 ° C holding time as a variable, through the corresponding results and analysis, optimize the selection of holding time.
2. Simulation results
(1) The temperature, strain and stress field of the step insulation period at 450 °C for 2 h are shown in Fig. 2. The temperature difference between the inside and outside of the rotary body is small, but there is stress concentration, mainly distributed in the grooves, steps and cores, most of the stress. Above 100 MPa, the local maximum is about 200 MPa. The temperature field, stress and strain at 650 °C for 2 h are shown in Fig. 3. The internal and external temperature difference is 15 °C. There is still stress concentration inside the rotor, and the stress level is reduced. Most of the stress is 50-100 MPa and the highest is about 120 MPa.
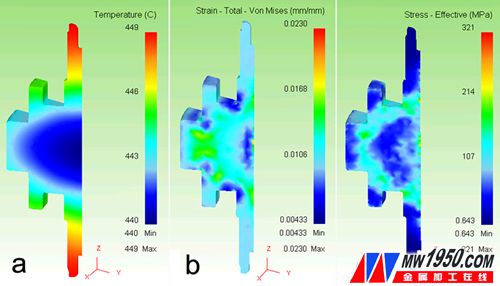
(a) Temperature (c) strain (d) stress field
Figure 2 Insulation at 450 ° C for 2 h
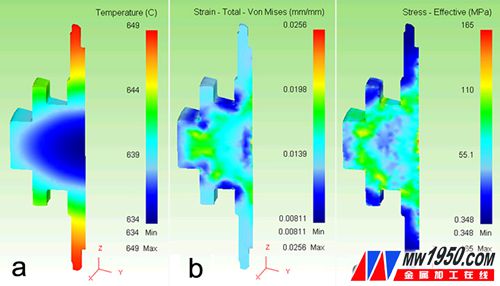
(a) temperature (c) strain (d) stress field
Figure 3 650 ° C insulation 2h
(2) Austenite transformation Initially, the austenite transformation initially has only a partial structural transformation in the upper part of the axon and step protrusion. Since the temperature rises faster at this time, the maximum temperature difference between the inside and the outside of the body is about 50 ° C, and the temperature difference between the outer diameter and the core is about 30 ° C. The stress is mainly concentrated in the grooves, steps and cores, and the stress level is low, up to 60-70 MPa.
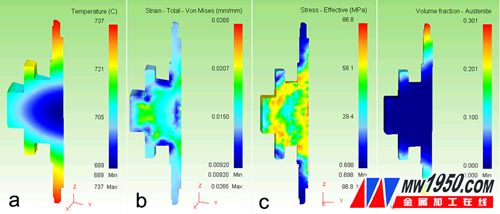
(a) temperature (b) strain (c) stress field (d) austenite transformation volume
Figure 4 Initial transformation of austenite
(3) After 850 °C heat preservation process, the temperature difference of the rotary body is further increased after 2 hours of heat preservation at 850 °C, but the stress level is very low, the austenite transformation volume is increased, and the austenite transformation of the stepped portion of the shaft portion and the groove portion is basically completed. The amount of austenite transformation in the middle is a function of the distance from the heart. At this time, the volume increase caused by thermal expansion and the volume reduction caused by the tissue transition tend to cancel the balance. After 4 hours of heat preservation at 850 °C, the temperature difference of the rotating body is still very large, about 60 ° C; however, the stress level is very low, less than 50 MPa; the austenite transformation of the shaft and step protrusion is complete, and the other parts are close to completion, both above 96%. . Compared to the volume reduction caused by the austenite transformation, the volume increase caused by thermal expansion predominates, and the volume expansion fraction of the rotor is 3.05%.
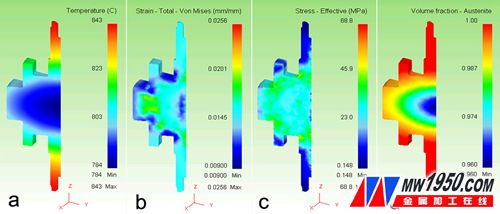
(a) temperature (b) strain (c) stress field (d) austenite transformation volume
Figure 5 850 ° C insulation 4h
(4) The austenite transformation is completed at 850 °C for 4 h and 50 min. The austenite transformation of the rotor is completed (Fig. 6). At this time, the temperature difference of the rotor is reduced by about 30 °C; the force level inside the rotor is further reduced. , below 40 MPa; the volume increase caused by thermal expansion is still dominant, and the volume expansion fraction of the revolving body is 3.17%. As the insulation is extended, the temperature difference is further reduced and the stress is also reduced, as shown in FIG. When the temperature is 850 °C for 7h, the internal and external temperature difference is only 5 °C, most of the stress is 20MPa, and the local maximum stress is also lower than 40MPa.
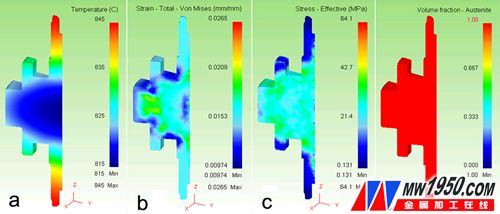
(a) temperature (b) strain (c) stress field (d) austenite transformation volume
Figure 6 End of austenite transformation
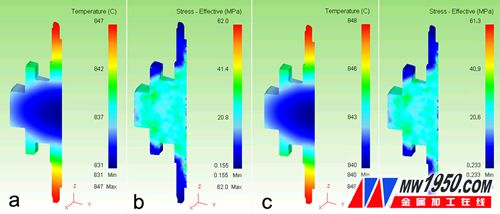
(a) Temperature (b) Stress field, 850 °C for 7 h (c) Temperature (d) Stress field
Figure 7 850 ° C insulation 6 h
3. Conclusion
In this paper, the temperature field and stress field change of the large-scale rotary forgings during the quenching heating process are taken as the research object. The 850 °C holding time is taken as the variable, and the 850 °C holding time is optimized by the results and analysis, in order to provide reference for the heat treatment process practice. The analysis found that there is a stress concentration inside the rotating body during the heating phase. The local stress can be up to 200 MPa during heating at 450 °C, and the stress level decreases with heating time, and gradually decreases below 100 MPa. During the heating at 850 °C, the stress level is further reduced. When the temperature is kept for 4h and 50min, the rotating body is completely transformed into austenite. The temperature difference between the inside and the outside is large, and the core temperature is only about 820 °C, which is lower than the furnace temperature. According to the results of the simulation analysis, the heating phase should be slowly heated to prevent product defects caused by excessive thermal stress. The recommended holding time is 6 to 6.5 hours. It has been proved by practice that after heating at 850 °C for 6.5 h, the grain size, metallographic structure and mechanical properties of the rotor after heat treatment, and the product qualification rate meet the requirements of the index.
Asphalt Cutting Disc,Cutting Asphalt With Angle Grinder,Angle Grinder Blade For Asphalt,Angle Grinder Asphalt Blade
Hengshi Diamond Tools CO.,LTD , https://www.ryomaltools.com